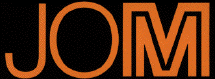 |
The following article is a component of the February 1998 (vol. 50, no. 2) JOM and is presented as JOM-e. Such articles appear exclusively on the web and do not have print equivalents.
|
Research Summary
Grain Refinement in Aluminum Alloys by Means of Electromagnetic Vibrations Including Cavitation Phenomena
Charles Vivès
 |
---|
CONTENTS |
---|
|
In this article, new magnetohydrodynamic methods of transmitting forced vibrations to solidifying aluminum-alloy melts are presented. It is shown that the cavitation threshold depends mainly on the electromagnetic pressure peak. In the presence of well developed cavitation situations, a very fine and homogeneous microstructure has been observed throughout the irradiated ingots. Several new prototypes allowing for significant energy savings that are likely to be used for industrial applications, including the elaboration of metal-matrix composites by means of a preform infiltration process, are described.
Owing to their impact on industrial casting processes, increasing interest has been shown during the past two decades in fundamental and applied investigations on metal solidification, either in the presence of free convection or when various dynamic treatments generating forced convection are applied in the melt during freezing.1-9 A number of examples can be found in the literature where external forces have been applied to induce fluid flow during solidification in order to refine grain size. These methods include rotation of the mold, mechanical or electromagnetic stirring of the melt, and rheocasting.1-12 Under these conditions, grain structures of castings and ingots change from columnar-dendritic to equiaxed dendritic or globular when they are solidified in the presence of a sufficiently intense forced convection, which generally promotes both the evacuation of superheat and the homogenization of the melt temperature. The phenomena occurring during these various treatments are currently well understood.
Several investigators have found that mechanical vibrations of both sonic and ultrasonic character, when applied during the solidification of metals and alloys, modify conventionally obtained macrostructures and microstructures.12-15 The most commonly observed effect is the suppression of undesirable dendritic and columnar zones and the development of a fine-grained equiaxed structure. In fact, the effects produced when high-intensity sonic or ultrasonic waves are propagated through molten metals can be listed under three main categories: grain refinement, dispersive effects, and degassing resulting in reduced porosity. In addition, it has been found that vibrations of a mechanical origin are effective in increasing fluidity by as much as a factor of three and consequently, favorably influence the mold-filling ability of aluminum alloys.16-17 There appear to be two distinct views regarding the mechanism, which may be explained by the cavitation effects and the influence of the fluid-flow phenomena.
Cavitation is the term used to describe the formation of bubbles, or cavities, in liquid. These cavities may be filled with air or vapor or may be almost empty; they can be produced in liquids by the passage of sonic or ultrasonic waves, provided they are of suitable frequency and intensity. Due to the oscillation of the medium, regions of compression and rarefaction are formed. In the rarefaction regions, a negative pressure (tension) may exist and air or vapor bubbles can form. In most liquid metals, a considerable amount of gas is present in the form of very small bubbles, which are, in most circumstances, seeded from pre-existing gas pockets.15,17,18 Liquid vapor may also evaporate into the partial void produced by the sudden expansion of the undissolved gas bubbles. The usefulness of cavitation in processes such as cleaning, dispersion, and grain refinement is largely due to the very high pressure produced locally on the collapse of the cavities. During this collapse time, the walls of the bubble are forced inward until they impinge on the small nuclei of gas or vapor contained in the cavity, which is severely compressed at the time. It has been demonstrated that the pressure in the bubbles immediately prior to their final collapse can reach several thousand atmospheres.15,18,19 Thus, when the bubbles finally disappear, extremely powerful shock waves occur, which are responsible for most of the phenomena brought about by cavitation. In particular, during metals and alloys solidification, the forces associated with cavitation result in the dislocation of growing crystals. This splitting up of crystals effectively produces many more nuclei around which new crystals can form. Thus, in this manner, the crystals never grow beyond a certain size.
 |
Figure 1. The principle of production of forced electromagnetic vibration in a solidifying melt. |
The other view is that vibrations also give rise to considerable agitation of the melt and result in the newly formed nuclei being distributed throughout the solidifying pool, so that crystallization takes place uniformly inside the entire volume. Moreover, the vibrations have much the same effect as turbulence, dispersing small crystals so that more of them grow, resulting in reduced grain size.
The sonic or ultrasonic irradiation of molten metals is mainly carried out with magnetostrictive, or piezoelectric, transducers (Figure 1). Coupling rods made of quartz, graphite, and various ceramic materials have been used to communicate vibrations to a molten metal, and these materials are attached to the transducer by special cements. However, such a technique presents several disadvantages. The oscillating rods are very rapidly dissolved when they are immersed into molten aluminum alloys, and this circumstance provokes an undesirable contamination of the metal. Moreover, the intensity of cavitation is greatest near the transducer or the coupling rod face; thus, the use of such a system is principally justified for the treatment of metal mixtures on a small scale.
EXPERIMENTAL PROCEDURES |
---|
|
 |
Figure A. A schematic of a system for the mechanoacoustic irradiation of melts. |
|
The principle used here consists of the simultaneous application of a stationary magnetic field Bo and a sinusoidal electric current of low frequency N and intensity i = I sin t during solidification of an alloy contained in a parallelepipedic tank. The width, height, and length of the vessel are represented by a, h, and L, respectively. In our experiment, the externally imposed horizontal electric and magnetic fields are perpendicular (Figure A). The alternating current density j = J sin t induced a periodic magnetic field b = B sin ( t + ) of the same frequency.20 From the hydrodynamic standpoint, the melt flow may be considered as the superposition of three motions: two alternating flows of N and 2N frequency, respectively, and an unstable recirculating flow that may be resolved into a steady component and a random component.
The externally imposed stationary magnetic field Bo interacts with the electric current of density j and gives rise to a vertically directed periodic electromagnetic force j x Bo of frequency N, which in turn forces the solidifying melt into vibration. The resultant vertical electromagnetic force applied to the whole melt volume is given by F = Bo I L sin t and generates an electromagnetic vibrating pressure
The crucible, whose internal dimensions were 2 cm x 4 cm x 12 cm, was made of stainless steel. In order to prevent spillout of the solidifying melt, particularly as it is vibrated at full electromagnetic power, the pool was hermetically closed by an upper horizontal wall. The combination of adjustable heating and cooling systems enabled regulation of the heat-extraction rate and, consequently, of the solidification time duration.
|
 |
Figure B. The influence of the vibrating electromagnetic pressure amplitude on the grain refinement at (a) coarse refinement (P = 0.25 bar), (b) refinement due to shear-rate effects (P = 0.52 bar), (c) the simultaneous influence of shear rate and cavitation (P = 0.84 bar), and (d) the predominance of cavitation effects, producing a fine microstructure (P = 1.40 bar). 1electromagnetic pressure amplitude, 2static pressure, and 3tension generated in liquid (negative pressure). The dotted line corresponds to the onset of a significant grain refinement provoked by the oscillating flow, and the hachured area corresponds to the critical threshold zone of cavitation. |
|
An alternating voltage of 50 Hz frequency was applied between the stainless-steel electrodes of 2 cm x 4 cm cross section, permitting the passage of a horizontal sinusoidal current through the solidifying alloy to take place. The current intensity I was modulated from 0-3,500 A (peak value). A horizontal, stationary, and nearly uniform magnetic field Bo, perpendicular to the current density j and likely to vary within the range 0-0.7 T, was imposed (Figure A). This device enabled achieving relatively high amplitudes J of the electric-current density, the electromagnetic body force j x Bo, and the electromagnetic pressure P. As an example, for I = 3,500 A and Bo = 0.7 T, the corresponding values of the main periodic parameters were J = 4.38 106 A.m-2, j x Bo = 3.06 106 N.m-3, and P = 122,500 Pa (i.e., 1.21 bar), whereas the ratio of the peak value of the vibrating electromagnetic force to the gravity force applied to the melt is on the order of 130.
In these experiments, the pressure in the solidifying liquid metal is the sum of static and oscillating terms (Figure B). Actually, the metallostatic pressure pgh' at depth h' and the fluctuating dynamic pressure 1/2 u2 can be neglected here. Accordingly, if the electromagnetic pressure amplitude is greater than the atmospheric pressure, then the pressure in the liquid will be negative (tension) for part of each period (Figure B-d).
On the other hand, velocity measurements21 showed that the fluctuating flow is relatively intense. When the electromagnetic pressure is optimal (1.21 bar), the shear rate du/da reaches 3 · 102 s-1, a value comparable to the magnitude order obtained in the rheocasting operation.9-11 It appears that during the irradiation of the semisolid alloy, the apparent viscosity remains practically unchanged up to a solid fraction on the order of 0.5, whereas the velocity decreases dramatically when the solid fraction exceeds 0.55.
The production of cavitation in liquid metals strongly depends on the most volatile undissolved gas content of the liquid, and it has been established that in the case of aluminum melts, the hydrogen content is the controlling factor.15,22 The solubility of hydrogen in aluminum is dependent on both the partial pressure of gas and the melt temperature. At a constant temperature, the equilibrium concentration of gas in solution is proportional to the square root of the partial pressure.22 For example, at a melt temperature of 650°C, the hydrogen level is on the order of 0.3 ppm, and the corresponding equilibrium pressure is 0.29 bar.22
Cavitation takes place with full efficiency during the negative pressure part of a cycle or a series of cycles (Figure B-d), and nucleation follows either as a result of the modification in equilibrium temperature, caused by the pressure change during the collapse of the cavitation bubbles, or as a result of cooling the surface of the bubbles by evaporation during its growth. Under this circumstance, cavitation may occur at several points inside the liquid and on the wall mold at a rate of 50 times per second.
|
The micrograph in Figure 2a, exhibits a typical columnar-dendritic structure corresponding to the as-cast A356 alloy. Figures 2b through 2f relate to the alloy solidification in the presence of increasing amplitudes of forced electromagnetic vibrations. Examination of Figure 2b, which is connected with the electromagnetic pressure peak displayed in Figure B-a (i.e., 0.25 bar) of the sidebar Experimental Procedures, reveals the presence of both coarse dendritic fragments and big clusters. It appears that the fluid-flow intensity (velocity peak on the order of 60 cm.s-1) is sufficient to prevent the formation of an interlocked network of dendritic shape. Examination of Figures 2c and 2d, which correspond to the electromagnetic pressure crest conveyed in Figure B-b, shows that the electromagnetic vibrations can refine the structure (average grain diameter of about 120 µm) even in the absence of cavitation. This observation can be interpreted by the extent of the hydrodynamic effects (velocity peak higher than 1 m s-1), which are quite similar to those encountered in the rheocasting techniques.9-11 Due to the intense oscillating flow and the high degree of turbulence, the whole volume of the semisolid mixture is practically isothermal. Consequently, the crystallization proceeds simultaneously throughout the undercooled melt around a number of suspended nuclei. This shearing process breaks dendritic particles and deforms them into a spheroidal shape9-11 (Figures 2c and 2d).
a |
 |
b |
 |
c |
 |
d |
 |
e |
 |
f |
 |
Figure 2. Microstructures of an A356 aluminum alloy in (a) the as-cast condition and as electromagnetically irradiated material at (b) P = 0.3 bar, (c) and (d) P = 0.52 bar (various magnifications), (e) P = 0.35 bar (applied during 10 min.) followed by P = 1.16 bar (applied during 15 s), and (f) P = 1.16 bar (applied during 12 min.). |
Figure 2e relates to the following test. First, an electromagnetic pressure amplitude of 0.35 bar was applied to the solidifying alloy for ten minutes from the liquidus temperature, with a cooling rate of 3.5°C mn-1. Next, a pressure peak of 1.16 bar was imposed suddenly through a rapid augmentation of the current intensity for a relatively short time (15 s), then the semisolid alloy was rapidly cooled by water at a rate of 100°C mn-1. In this experiment, the first operation corresponds to grain refinement, consisting mainly of the presence of an agglomeration of nondendritic crystals and due only to hydrodynamic effects in the absence of cavitation phenomena, whereas the second operation is executed under the cavitation conditions. The presence, indicated by arrows, of an area of about 600 µm mean diameter composed of much smaller grains and a crack propagating along a distance of approximately 1 mm can be seen. This observation is understood by the disintegration of a cluster, which gives rise to the formation of about 500 crystals of 40 µm average diameter, probably under the action of a single cavitation event producing impressive mechanical damage over a microscopic region. Identical repetitive tests have confirmed this observation. In such a case, where the irradiation time is rather short, cavitation in the solidifying two-phase mixture does not take place uniformly, and systematic trials showed that the regions of intense cavitation are quite random from one experimental run to the next.
The microstructure displayed in Figure 2f has been obtained from a trial performed in the presence of electromagnetic vibrations related to the cavitation conditions. Negative pressure peaks of 1.16 bar were transmitted 50 times per second for 12 minutes to the solidifying melt from the liquidus at a cooling rate of 4°C mn-1. Examination of Figure 2f reveals that the grains are much finer (50 µm mean grain size) and less globular than those produced by the hydrodynamic effect in the absence of cavitation (Figures 2c and 2d). Moreover, it is seen that the cavitation effects result in the total disappearance of the numerous large clusters observed in Figures 2b through 2e.
 |
Figure 3. Macrostructures of a 1050 aluminum alloy (a) conventionally cast and (b) electromagnetically irradiated during 12 min., P = 1.16 bar. The width of the samples is 22 mm. |
 |
Figure 4. The magnetohydrodynamic cavity resonator. |
 |
Figure 5. Determination of the resonant frequency related to the magnetohydrodynamic cavity resonator prototype. The normalized pressure P* is the ratio of the amplitude pressure at the frequency N to the amplitude pressure at the frequency N = 50 Hz. |
 |
Figure 6. A schematic of preform infiltration by means of vibrations produced in a magnetohydrodynamic resonant cavity. |
Similar results concerning a significant reduction of the grain size under the action of the cavitation phenomena were obtained on a 2024 aluminum alloy.23,24 The macrographs in Figure 3 reveal the dramatic reduction of the macrograin size of an electromagnetically irradiated 1050 aluminum alloy characterized by a relatively narrow solidification interval. It appears that contrary to the case of mechanically vibrated melts,12 the electromagnetically irradiated semisolid alloy mixtures exhibit uniform grain refinement across the entire section. This is due to the fact that in this experiment, the electromagnetic forces that induce oscillating motion act uniformly throughout the semisolid melt. Moreover, it should be noted that the cavitation effects, which are exclusively provoked by the electromagnetic-pressure fluctuations, are likely to be effective even after the arrest of the two-phase mixture motion, provided that gas bubbles remain inside the melt and upon the crucible walls.
Furthermore, it has been remarked that despite the presence of a draft angle between the vertical walls of the crucible, the mold stripping of the electromagnetically vibrated alloys was extremely difficult. This finding may be understood by the fact that the semisolid alloy mixture is rather rapidly solidified from a high solid fraction of 0.65, corresponding to the completion of the melt oscillations, and also because cavitation causes efficient degassing, resulting in tremendously reduced shrinkage and porosity. Consequently, the compactness of the irradiated material is considerably improved.
This process presents a serious drawback for very important potential industrial applications (which consist of alloy-grain refinement), since, for the large-scale ingot castings, substantial energy consumption is required to reach the cavitation threshold. Indeed, it is not easy to apply relatively intense steady magnetic-field strength inside an air gap on the order of 30 cm width and to inject current intensity of about 40,000 A.
Another technique consisting of the continuous adjustment of the electromagnetic vibration frequency in order to maintain the melt at resonance can be considered. Under this condition, the magnetic-field strength and the electric-current intensity would be markedly lowered, and, consequently, the facility cost and energy expense would be decidedly reduced.
This alternative solution can be forced by means of the extension of the principle of the Helmoltz resonator25-27 to magnetohydrodynamics. The Helmoltz resonator consists of a bottle almost entirely enclosing a volume of air, with a small opening constituting a coupling between the air in the bottle and the external air of the room. The exact form of the cavity is unimportant; it may be spherical or cylindrical, provided that the smallest dimension is considerably greater than the dimensions of the aperture.25-27 Moreover, the dimensions of the resonator are small compared with the wavelength of sound at which it will resonate.
The working principle of this new magnetohydrodynamic resonator (Figure 4) is nearly analogous to the Helmoltz resonator. This new resonator consists of a cavity containing a liquid metal, where the neck is crowned by a small pulsating electromagnetic pump; this pump plays the role of an exciter for the resonant cavity. An alternating voltage of frequency N is applied between the two electrodes while the pump is subjected to a stationary magnetic field Bo perpendicular to the variable electric current.
The behavior of the resonator has been investigated by means of a small laboratory model. The variation of the electric-current pulsation by using a frequency generator allowed the detection of the maximum value of the electromagnetic pressure inside the cavity, measured by means of a piezoelectric sensor and corresponding to the resonance frequency. Since the elastic modulus of the liquid metal and the cavity wall made of stainless steel were on the same order, the resonance that was reached at N = 824 Hz cannot be extremely sharp. However, if all other conditions remain unchanged (i.e., the same magnetic-field strength and electric-current intensity), the amplitude of the vibrating pressure in the cavity increases by a factor of about ten with respect to the pressure generated by a 50 Hz voltage frequency (Figure 5). In view of this result, the prospect of using this device for metallurgical applications seems all the more hopeful as these peak pressures are generated in a much larger volume with regard to the dimensions of the pulsating electromagnetic pump.
It has been demonstrated that sonic or ultrasonic vibrations of mechanical origin have both been effective in increasing fluidity by as much as a factor of three.16,17 Fluidity is the ability of a molten metal to fill very narrow spaces, whether in a mold cavity (thin-wall castings) or in the gap between the reinforcement fibers in cast composites, for example. Moreover, vibrations promote wetting of reinforcement by metallic melts as a result of partial desorption of absorbed gases from the surface of the particles.15
Infiltration techniques are commonly used to fabricate metal-matrix composites.28,29 These infiltration processes involve holding a fiber preform of the reinforcing phase within a mold and infiltrating it with molten metal in order to produce a composite material. Liquid metal does not spontaneously wet the reinforcement; hence, it is generally forced into the preform by means of an externally applied pressure that overcomes the capillary and fluid-drag forces.
Accordingly, it appears that a novel approach of infiltration technology can be considered. This method consists of infiltrating the preform with an aluminum alloy, with the assistance of vibratory electromagnetic pressure generated by the magnetohydrodynamic Helmoltz resonator. The study of the ability of this new process, which is schematically presented in Figure 6, is currently in progress.
 |
Figure 7. The principle of electromagnetic vibration production in molten metals using a noncontact method. |
An alternative method consists of the simultaneous application of a stationary magnetic field Bo and a variable magnetic field b in the molten metal during the course of solidification (Figure 7); these magnetic fields are nearly parallel to the vertical axis of the ingot. The stationary magnetic field is generated by at least one coil that is supplied with direct current. The alternating magnetic field is created by another inductor, which is of similar geometry, supplied with an alternating current of frequency N. Under the effect of the periodic current, the inductor generates a variable field b in the melt, which in turn, gives rise to an induced periodic current of density j.
The combined action of the colinear fields generates vibrations in the metal pool, which are of a double origin. The interaction of Bo and j engenders a vibrating force of frequency N, whereas the j x b force consists of a time-independent component and an oscillatory component of frequency 2N. The electromagnetic vibrations mainly originate inside the electromagnetic-skin depth area and owing to the medium elasticity, are propagated throughout the melt. The solidifying alloys can be irradiated by magnetoacoustic waves vibrating at the fundamental resonance frequency. The capability of this method for use in industrial applications (e.g., the grain refinement of aluminum alloys in continuous casting and permanent mold casting) has been recently examined.24
The irradiation of metallic melts by sonic or ultrasonic waves favorably influences grain refinement, dispersive effect, mixing, degassing, and mold filling. With regard to mechanical vibrations, electromagnetic vibrations present the advantage of acting uniformly and practically at will without material contact with the melt and, consequently, without risk of contamination. Obviously, the experimental findings reported here do not exhaust this very promising subject, and more thorough investigations are currently underway. This work mainly investigates the optimal conditions for the irradiation of solidifying alloys by magnetoacoustic waves vibrating at the fundamental resonance frequency.
1. F.C. Langenberg, G. Pestel, and C.R. Honeycutt, Trans. of the Met. Soc. of AIME, 221 (1961), p. 993.
2. W. Poppmerier, B. Tarmann, and O. Schaaber, J. Met., 18 (4) (1966), p. 1109.
3. H.S. Man., Iron and Steel Int., 2 (1979), p. 29.
4. G. Abbaschian and S. David, Trans. of the Metall. Soc. of AIME, 1 (1983), p. 3.
5. A. Tsavaras and H. Brody, J. Met., 36 (3) (1984), p. 31.
6. C. Vivès and C. Perry, Int. J. Heat Mass Transfer, 1 (1986), p. 21.
7. C. Vivès, Metall. Trans. B, 20B (1989), p. 623.
8. C. Vivès, Metall. Trans. B, 20B (1989), p. 631.
9. M.C. Flemings, Metall. Trans. B, 22B (1991), p. 269.
10. C. Vivès, Metall. Trans. B, 23B (1992), p. 189.
11. C. Vivès, Metall. Trans. B, 24B (1993), p. 493.
12. J.-P. Gabathuler et al., Processing of Semi-Solid Alloys and Composites, ed. S.B. Brown and M.C. Flemings (Cambridge, MA: MIT, 1992), p. 33.
13. D. Goel, D. Shunkla, and P. Pandey, Trans. of Indian Institute of Metals, 3 (1980), p. 196.
14. J. Campbell, Int. Met. Reviews, 2 (1981), p. 71.
15. O. Abramov, Ultrasound in Liquid and Solid Metals (Boca Raton, FL: CRC Press, 1994), p. 289.
16. M.C. Flemings et al., AFS Transactions, 70 (1962), p. 1029.
17. F.R. Mollard, M.C. Flemings, and E.F. Niyama, J. Met., 39 (11) (1987), p. 34.
18. T. Leighton, The Acoustic Bubble (London: Academic Press Ltd, 1994), p. 531.
19. J. Szekely, Fluid Flow Phenomena in Metals Processing (New York: Academic Press Ltd, 1979), p. 305.
20. J. Shercliff, A Textbook of Magnetohydrodynamics (Oxford, U.K.: Pergamon Press, 1986), p. 44.
21. C. Vivès, Int. J. Heat Mass Transfer, 33 (1990), p. 2585.
22. D. Lillicrap, Electrowärme International, 44 (1986), p. 116.
23. C. Vivès, Metall. Trans. B, 27B (1996), p. 445.
24. C. Vivès, Metall. Trans. B27B (1996), p. 456.
25. A.B. Wood, A Textbook of Sound (London: G. Bell and Sons Ltd, 1964), p. 197.
26. T. Hucter and R. Bolt, Sonics (New York: John Wiley and Sons, 1966), p. 325.
27. W. Elmore and M. Heald, Physics of Waves (New York: McGraw-Hill, 1969), p. 148.
28. R.M. Bhagat, Metal Matrix Composites: Processing and Interfaces (New York: Academic Press Ltd, 1991), p. 43.
29. B. Vyas and C. Preece, J. Appl. Phys., 47 (1976), p. 5133.
ABOUT THE AUTHOR
Charles Vivès earned his Ph.D. in magnetohydrodynamics at the University of Algiers in 1963. He is currently a professor at the Universite d'Avignon. Dr. Vivès is also a member of TMS.
For more information, contact Charles Vivès, 33.we Louis Pasteur, Universite d'Avignon, F 84000, Avignon, France; telephone (33) 04 901 44461; fax (33) 04 908 63876.
Copyright held by The Minerals, Metals & Materials Society, 1998
Direct questions about this or any other JOM page to jom@tms.org.