Research Summary
A Lower-Melting-Point Solder Alloy for Surface Mounts
M.T. McCormack, Y. Degani, H.S. Chen, and W.R. Gesick
CONTENTS
Significant manufacturing cost reductions can be realized with
lower-temperature surface mount processing by increasing yields and using less
expensive components and boards. A lower-melting-point solder alloy (nominal
composition Sn-41.75Pb-8Bi-0.5Ag) has been developed that enables significant
reductions in peak reflow temperatures during surface-mount assembly. The
solder alloy is compatible with standard Pb-Sn surface finishes, melts within
the temperature range of ~166-172°C, and has promising mechanical
properties.
Many electronics manufacturers are implementing less expensive components
and/or circuit board materials in product assembly in order to reduce
production costs. This practice often introduces manufacturing yield problems
because the less expensive materials tend to be more sensitive to temperature
and moisture. For example, moisture-sensitive plastic-surface mount devices
(MSDs) are susceptible to moisture-induced damage during the soldering
process.1-5 When plastic packages are exposed to
ambient conditions,
they diffusively absorb moisture through the plastic-molding compound. This
moisture can subsequently condense at internal interfaces (e.g., between the
plastic and the silicon die or between the lead frame and the plastic). The
solder reflow temperature profile may then cause this condensed moisture to
rapidly evaporate. The volume increase of the moisture associated with the
phase change to vapor may exert significant pressures at internal interfaces
while the plastic molding compound simultaneously experiences a strength
reduction because of the elevated temperatures. This combination of factors,
often called the popcorn effect, can cause delaminations or cracks that may be
difficult to detect. Extended cracks breaking out to the external surface of
the package can provide paths for process chemicals such as flux or cleaning
agents and contaminants in the atmosphere known to compromise device
reliability.
Other failure modes include lifted, sheared, or weakened wire bonds. Some of
these "popcorn"-related failures are immediate and show up in electrical
testing, while others are more subtle and cause field failures. This moisture
susceptibility limits the factory floor life of MSDs at a given factory's
ambient temperature and relative humidity.
In order to alleviate these yield problems, there is a push to lower peak
reflow temperatures during surface mount assembly; however, reducing the peak
reflow temperature when using eutectic Sn-37Pb solder usually results in
unacceptable occurrences such as insufficient pad wetting, poor fillet
geometries, solder balling of the paste during reflow, partial reflow due to
the thermal mass of components, or no reflow at all.
The most common alloy used in reflow soldering is eutectic Sn-37Pb. Since
this alloy has a melting point of 183°C, there are practical lower
limits to the solder-reflow temperature. For example, the peak top-side board
temperature in
most surface-mount oven profiles varies, depending on the application, between
205-220°C in order to enable Pb-Sn eutectic solder pastes to reflow and
form acceptable soldered joints. Therefore, a reliable lower-melting-point,
drop-in
solder is desired.
Alternative solder alloys with lower melting points than those of eutectic
Sn-37Pb are often considered for applications such as those described; the
alternate alloy most frequently considered is Sn-43Pb-14Bi. This solder has
several attributes that are not desirable for all applications; the foremost
among these are the wide range of melting and the lower solidus temperature.
Figure 1a is a typical differential scanning calorimetry (DSC) profile of the
Sn-43Pb-14Bi alloy upon heating at a scanning rate of 5°C/min. The profile
shows two separate regions of heat extraction that are indicative of melting.
In the lower temperature region, a large portion of the alloy (~30%) melts
sharply at approximately 137°Cthe melting point of the Bi-42Sn eutectic
alloy. This initial solidus temperature is followed by discontinuity in the DSC
curve that is indicative of an initial liquidus temperature at ~147°C. The
majority of the alloy volume remains solid until approximately 165°C,
denoted in Figure 1a by a discontinuous slope change on the premelting
(solid-state diffusion) portion of the second heat extraction well. This
temperature of 165°C is, in effect, a second solidus temperature for the
remaining solid portion of the alloy. The majority of the alloy finally becomes
molten at approximately 170°C (another effective liquidus temperature). A
small residual portion (~5-10%) of the alloy does not completely melt until
approximately 178°C. This wide range of melting can not only introduce
handling difficulties in manufacturing, but the lower solidus temperature at
138°C can contribute to lower thermal fatigue resistances.
Figure 1. Typical differential scanning calorimetry (DSC) profiles
upon heating at a scanning rate of 5°C/min. for
(a) Sn-43Pb-14Bi, (b) Sn=-42Pb-8Bi, and (c) Sn-41.75Pb-8Bi-0.5Ag. |
---|
a | b | c |
---|
 | 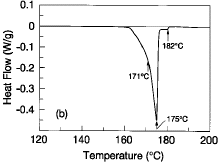 | 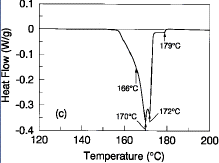 |
An alternative solder alloy composition with a lower melting point than
eutectic Sn-37Pb has been developed. The goal of this work was to determine a
ternary Sn-Pb-Bi that not only melted at least 10°C below that of eutectic
Sn-37Pb, but was also free of the ~138°C melting phases and had a narrow
range of melting (~10°C). The best compromise of thermal character was found
in the Sn-42Pb-8Bi ternary composition. Figure 1b is a typical DSC profile of
the Sn-42Pb-8Bi alloy at a scanning rate of 5°C/min. As can be seen by a
discontinuous slope change on the premelting portion of the heat extraction
well, the solidus temperature of this alloy is ~171°C. The primary liquidus
temperature is ~175°C; there is a very small (approximately 2-3%) residual
amount of solids that do not completely melt until 182°C. Compositional
fluctuations well over a percent are required to significantly alter the
melting character shown. For this composition, excess bismuth results in the
~138°C melting phases; excess tin and lead result in residual solids beyond
the 183°C melting point of Sn-37Pb.
After establishing an optimum ternary composition of Sn-42Pb-8Bi, quaternary
additions were examined for additional beneficial effects on the melting
character of the alloy. Silver additions were the most beneficialpeak thermal
and mechanical benefits were obtained at ~0.5%Ag content. Figure 1c is a
typical DSC melting profile of the Sn-41.75Pb-8Bi-0.5Ag alloy at a scanning
rate of 5°C/min. The solidus temperature of this alloy is ~166°C, the
primary liquidus temperature is ~172°C, and there is a very small
(approximately 2-3%) residual amount of lead-rich solids that do not completely
melt until 178°C. This melting character suggests that it may be feasible to
lower peak reflow temperatures in surface mount assembly processes by as much
as 10-15°C using the silver-doped alloy. Compositional fluctuations of
silver below 0.2% are not effective in providing melting point depressions and
silver contents in excess of 0.8% begin to form phases with melting points well
beyond that of eutectic 63Sn-37Pb.
Figure 2. Scanning electron micrographs of (a) the ternary Sn-42Pb-8Bi and (b) Sn-41.75Pb-8Bi-0.5Ag as-cast microstructures. The microstructural
refinement is due to the silver addition in the quaternary alloy. |
---|
a | b |
---|
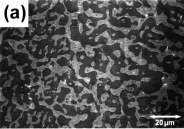 | 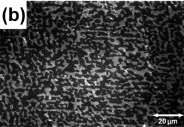 |
In addition to changing the alloy-melting character, the introduction of
0.5%Ag also appears to refine the as-cast microstructure. In the scanning
electron micrographs shown in Figure 2, the light contrast phase is lead-rich
and the dark contrast phase is tin-rich. The microstructural refinement can be
clearly seen between the as-cast ternary and quaternary alloys in Figures 2a
and 2b, respectively. The mechanical properties of the quaternary Sn-Pb-Bi-Ag
alloy are compared with those of two binary eutectic soldersSn-37Pb (melting
point = 183°C) and Sn-3.5Ag (melting point = 221°C)in the tensile
stress-strain data shown in Figure 3. The good strength and ductility
demonstrated by this alloy is very promising for thermal fatigue resistance.
Further work in this area is in progress.
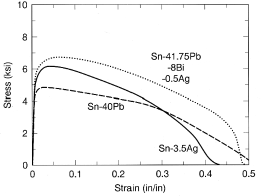 |
Figure 3. Comparative tensile stress-strain data performed at strain rates of 0.001/s for Pb-37Sn, Ag-3.5Ag, and Sn-41.75Pb-8Bi-0.5Ag solder specimens.
|
---|
Since the actual utility of the Sn-41.75Pb-8Bi-0.5Ag alloy will be, in large
part, determined by its reflow performance in lower-temperature surface mount
assembly, a no-clean RMA solder paste was manufactured. Both the
Sn-41.75Pb-8Bi-0.5Ag alloy and a standard eutectic Sn-37Pb paste (using the same
flux vehicle) were printed in 6.35 mm diameter circular features of 0.25 mm
height upon non-wettable Al2O3 substrates. Using a nitrogen-convection reflow
oven and monitoring the top-side substrate temperature with a calibrated
thermocouple, these test coupons underwent a thermal profile (Figure 4). The peak
top-side substrate temperature in this reflow profile is 179°C. The
alternative alloy (Figure 5a) exhibits excellent paste reflow that is free of
solder balls; the Sn-37Pb (Figure 5b) paste did not reflow at all.
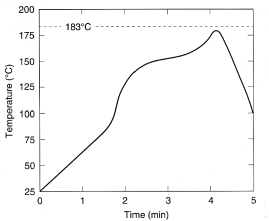 |
Figure 4. Top-side board temperature profile. The peak top-side temperature
in this reflow profile is 179°C.
|
---|
A similar experiment was then performed on FR-4 printed test coupons. The
circuit pads on the test coupons have a standard eutectic Sn-37Pb hot-air
solder-leveled (HASL) surface finish. After screen printing pastes of
Sn-41.75Pb-8Bi-0.5Ag and Sn-37Pb alloys on separate test coupons, capacitors
(also having eutectic Sn-37Pb contact surface finishes) were placed on the
pads. In the same manner as described above, the coupons underwent a monitored
reflow profile with a 179°C peak top-side board temperature. The
Sn-41.75Pb-8Bi-0.5Ag alloy (Figure 5c) again exhibits excellent paste reflow
and fillet formation free of solder balls, while the Sn-37Pb paste (Figure 5d)
does not reflow at all. Experiments with peak top-side board temperatures below
179°C over the same timeframe exhibited only partial reflow in the
Sn-41.75Pb-8Bi-0.5Ag alloy paste and are not recommended.
Figure 5. (a) The Sn-41.75Pb-8Bi-0.5Ag alloy paste and (b) a standard eutectic Sn-37Pb paste printed upon a non-wettable Ar2O3
substrate. Note that the Sn-37Pb paste did not reflow at all. Using the reflow
oven profile described in Figure 4 in a surface mount trial with capacitors
(Sn-37Pb contact surface finishes) on HASL-finished FR-4 test coupons, (c) the
Sn-41.75Pb-8Bi-0.5Ag alloy exhibits excellent paste reflow and fillet formation
that is free of solder balls and (d) the Sn-37Pb paste does not reflow at
all. |
---|
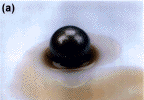 | 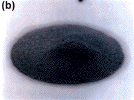 |  | 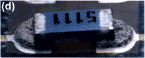 |
Factory trials using the solder have also proven very successful. Figures 6a
and 6b show J-leaded and 0.5 mm fine-pitch surface mount components,
respectively, that were monitored during reflow and experienced peak top-side
board temperatures of 179°C. The soldered components exhibit excellent
fillet formation with no bridging between leads.
Figure 6. (a) J-leaded and (b) 0.5 mm fine-pitch surface-mount components that
were monitored during reflow to have experienced peak top-side board
temperatures of 179°C. |
---|
a | b |
---|
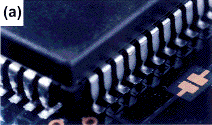 | 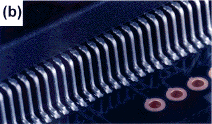 |
Experiments with fully populated boards having greater local thermal masses
are in progress to determine the lowest peak reflow temperatures for given
applications. However, it does seem quite clear that surface mount soldering
with a Sn-41.75Pb-8Bi-0.5Ag solder paste can be done at temperatures
significantly lower than those currently in use in order to relieve many yield
problems associated with moisture and temperature sensitivity in surface mount
assembly.
1. JEDEC Standard JESD22-A112, "Moisture-Induced Stress Sensitivity for Plastic Packaged Surface Mount Devices" (1994).
2. JEDEC Standard JESD22-A113-A, "Preconditioning of Plastic Surface Mount Devices Prior to Reliability Testing" (1995).
3. IPC-SM-786A, "Procedures for Characterizing and Handling of Moisture/Reflow Sensitive IC's" (Lincolnwood, IL, 1995).
4. M. Kitano et al., "Analysis of Package Cracking During Reflow Soldering Process," Proc. 17th Int. Sym. Testing & Failure Analysis (1991), pp. 213-220.
5. G. S. Ganesan and H. M. Berg, "Model and Analyses for Solder Reflow Cracking Phenomenon in SMT Plastic Packages," IEEE Trans. CHMT, 16 (8) (1993), pp. 940-948.
ABOUT THE AUTHORS
M.T. McCormack earned his Ph.D. in materials
science and engineering at University of California-Berkeley in 1991. He is currently a technical staff member at Bell Laboratories, Lucent Technologies. He is a member of TMS.
Y. Degani earned his Ph.D. in chemistry at Hebrew University of Jerusalem in 1985. He is currently a technical staff member at Bell Laboratories, Lucent Technologies.
H.S. Chen earned his Ph.D. in applied physics at Harvard in 1967. He is currently a technical staff member at Bell Laboratories, Lucent Technologies.
W.R. Gesick earned his B.S. in engineering science at New York University in 1968. He is currently president of Advanced Metals Technology and Amtech.
For more information, contact M.T. McCormack, AT&T Bell Laboratories, 600 Mountain Avenue, Murray Hill, New Jersey 07974; (908) 582-3547.
Copyright held by The Minerals, Metals & Materials Society, 1996
Direct questions about this or any other JOM page to jom@tms.org.